மோசமான நீர் எதிர்ப்பு, சீரற்ற மேற்பரப்பு, அதிக தூள் உள்ளடக்கம் மற்றும் சீரற்ற நீளம்? நீர்வாழ் தீவன உற்பத்தியில் பொதுவான சிக்கல்கள் மற்றும் மேம்பாட்டு நடவடிக்கைகள்.
எங்கள் அன்றாட நீர்வாழ் தீவன உற்பத்தியில், பல்வேறு அம்சங்களில் சில சிக்கல்களை நாங்கள் சந்தித்துள்ளோம். அனைவருடனும் விவாதிக்க சில எடுத்துக்காட்டுகள் இங்கே:
1, சூத்திரம்
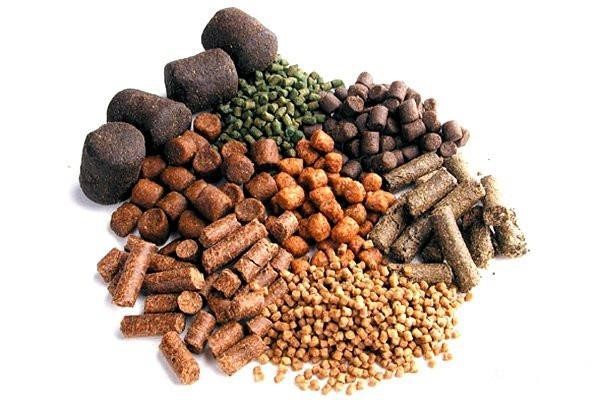
1. மீன் தீவனத்தின் சூத்திர அமைப்பில், கச்சா நார்ச்சத்துக்குச் சொந்தமான ராப்சீட் உணவு, பருத்தி உணவு போன்ற உணவு மூலப்பொருட்களின் வகைகள் அதிகம் உள்ளன. சில எண்ணெய் தொழிற்சாலைகள் மேம்பட்ட தொழில்நுட்பத்தைக் கொண்டுள்ளன, மேலும் எண்ணெய் அடிப்படையில் மிகக் குறைந்த உள்ளடக்கத்துடன் உலர்வாக வறுத்தெடுக்கப்படுகிறது. மேலும், இந்த வகையான மூலப்பொருட்கள் உற்பத்தியில் எளிதில் உறிஞ்சப்படுவதில்லை, இது கிரானுலேஷனில் அதிக தாக்கத்தை ஏற்படுத்துகிறது. கூடுதலாக, பருத்தி உணவை நசுக்குவது கடினம், இது செயல்திறனை பாதிக்கிறது.
2. தீர்வு: ராப்சீட் கேக்கின் பயன்பாடு அதிகரிக்கப்பட்டுள்ளது, மேலும் அரிசி தவிடு போன்ற உயர்தர உள்ளூர் பொருட்கள் சூத்திரத்தில் சேர்க்கப்பட்டுள்ளன. கூடுதலாக, சூத்திரத்தில் தோராயமாக 5-8% பங்களிக்கும் கோதுமை சேர்க்கப்பட்டுள்ளது. சரிசெய்தல் மூலம், 2009 இல் கிரானுலேஷன் விளைவு ஒப்பீட்டளவில் சிறந்தது, மேலும் ஒரு டன்னுக்கு மகசூலும் அதிகரித்துள்ளது. 2.5 மிமீ துகள்கள் 8-9 டன்களுக்கு இடையில் உள்ளன, இது கடந்த காலத்துடன் ஒப்பிடும்போது கிட்டத்தட்ட 2 டன்கள் அதிகரித்துள்ளது. துகள்களின் தோற்றமும் கணிசமாக மேம்பட்டுள்ளது.
கூடுதலாக, பருத்தி விதை மாவை நசுக்கும் திறனை மேம்படுத்த, பருத்தி விதை மாவையும் ராப்சீட் மாவையும் 2:1 விகிதத்தில் கலந்து நசுக்கினோம். முன்னேற்றத்திற்குப் பிறகு, நொறுக்கும் வேகம் அடிப்படையில் ராப்சீட் மாவின் நசுக்கும் வேகத்திற்கு இணையாக இருந்தது.
2, துகள்களின் சீரற்ற மேற்பரப்பு
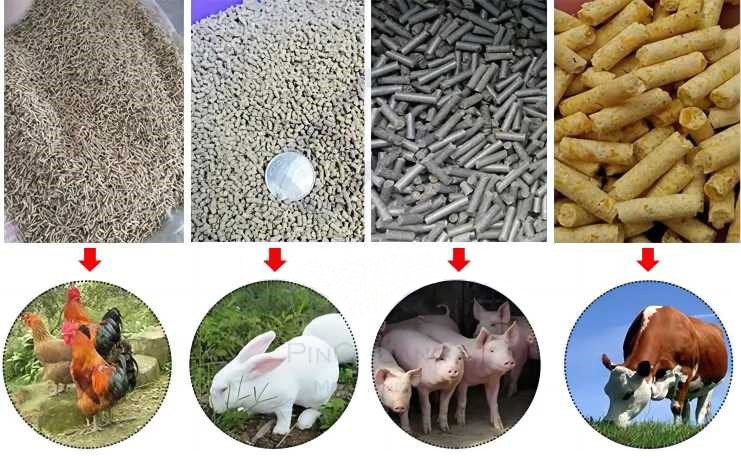
1. இது முடிக்கப்பட்ட பொருளின் தோற்றத்தில் பெரும் தாக்கத்தை ஏற்படுத்துகிறது, மேலும் தண்ணீரில் சேர்க்கப்படும்போது, அது சரிந்துவிடும் மற்றும் குறைந்த பயன்பாட்டு விகிதத்தைக் கொண்டுள்ளது. முக்கிய காரணம்:
(1) மூலப்பொருட்கள் மிகவும் கரடுமுரடாக நசுக்கப்படுகின்றன, மேலும் வெப்பநிலை மாற்றும் செயல்பாட்டின் போது, அவை முழுமையாக முதிர்ச்சியடைந்து மென்மையாக்கப்படுவதில்லை, மேலும் அச்சு துளைகள் வழியாக செல்லும்போது மற்ற மூலப்பொருட்களுடன் நன்கு இணைக்க முடியாது.
(2) அதிக கச்சா நார்ச்சத்து கொண்ட மீன் தீவன சூத்திரத்தில், வெப்பநிலைப்படுத்தும் போது மூலப்பொருளில் நீராவி குமிழ்கள் இருப்பதால், துகள் சுருக்கத்தின் போது அச்சுக்கு உள்ளேயும் வெளியேயும் உள்ள அழுத்த வேறுபாட்டின் காரணமாக இந்த குமிழ்கள் உடைந்து, துகள்களின் மேற்பரப்பு சீரற்றதாகிறது.
2. கையாளுதல் நடவடிக்கைகள்:
(1) நொறுக்கும் செயல்முறையை முறையாகக் கட்டுப்படுத்தவும்.
தற்போது, மீன் தீவனத்தை உற்பத்தி செய்யும் போது, எங்கள் நிறுவனம் 1.2மிமீ சல்லடை மைக்ரோ பவுடரை மொத்த மூலப்பொருளாகப் பயன்படுத்துகிறது. நசுக்கலின் நேர்த்தியை உறுதி செய்வதற்காக, சல்லடையின் பயன்பாட்டின் அதிர்வெண் மற்றும் சுத்தியலின் தேய்மான அளவை நாங்கள் கட்டுப்படுத்துகிறோம்.
(2) நீராவி அழுத்தத்தைக் கட்டுப்படுத்தவும்
சூத்திரத்தின்படி, உற்பத்தியின் போது நீராவி அழுத்தத்தை நியாயமான முறையில் சரிசெய்யவும், பொதுவாக 0.2 ஐ கட்டுப்படுத்தவும். மீன் தீவன சூத்திரத்தில் அதிக அளவு கரடுமுரடான நார் மூலப்பொருட்கள் இருப்பதால், உயர்தர நீராவி மற்றும் நியாயமான வெப்பநிலை நேரம் தேவைப்படுகிறது.
3, துகள்களின் மோசமான நீர் எதிர்ப்பு
1. இந்த வகையான பிரச்சனை நமது அன்றாட உற்பத்தியில் மிகவும் பொதுவான ஒன்றாகும், பொதுவாக இது பின்வரும் காரணிகளுடன் தொடர்புடையது:
(1) குறுகிய பதப்படுத்தும் நேரம் மற்றும் குறைந்த பதப்படுத்தும் வெப்பநிலை சீரற்ற அல்லது போதுமான பதப்படுத்தல் இல்லாமை, குறைந்த அளவு பழுக்க வைப்பது மற்றும் போதுமான ஈரப்பதம் இல்லாமைக்கு வழிவகுக்கிறது.
(2) ஸ்டார்ச் போன்ற போதுமான பிசின் பொருட்கள் இல்லாதது.
(3) வளைய அச்சின் சுருக்க விகிதம் மிகவும் குறைவாக உள்ளது.
(4) சூத்திரத்தில் எண்ணெய் உள்ளடக்கம் மற்றும் கச்சா நார் மூலப்பொருட்களின் விகிதம் மிக அதிகமாக உள்ளது.
(5) நொறுக்கும் துகள் அளவு காரணி.
2. கையாளுதல் நடவடிக்கைகள்:
(1) நீராவியின் தரத்தை மேம்படுத்துதல், ரெகுலேட்டரின் பிளேடு கோணத்தை சரிசெய்தல், வெப்பநிலை நேரத்தை நீட்டித்தல் மற்றும் மூலப்பொருட்களின் ஈரப்பதத்தை சரியான முறையில் அதிகரித்தல்.
(2) சூத்திரத்தை சரிசெய்து, ஸ்டார்ச் மூலப்பொருட்களை சரியான முறையில் அதிகரிக்கவும், கொழுப்பு மற்றும் கச்சா நார் மூலப்பொருட்களின் விகிதத்தைக் குறைக்கவும்.
(3) தேவைப்பட்டால் பிசின் சேர்க்கவும். (சோடியம் சார்ந்த பெண்ட்டோனைட் குழம்பு)
(4) சுருக்க விகிதத்தை மேம்படுத்தவும்ரிங் டை
(5) நன்றாக நொறுக்குவதன் நுணுக்கத்தைக் கட்டுப்படுத்தவும்.
4, துகள்களில் அதிகப்படியான தூள் உள்ளடக்கம்
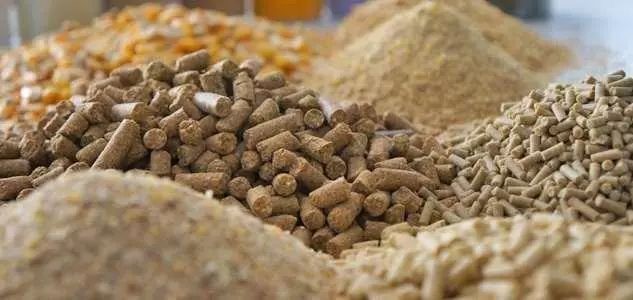
1. குளிரூட்டலுக்குப் பிறகும், திரையிடுவதற்கு முன்பும் பொதுவான துகள் தீவனத்தின் தோற்றத்தை உறுதி செய்வது கடினம். துகள்களில் அதிக சாம்பல் மற்றும் தூள் இருப்பதாக வாடிக்கையாளர்கள் தெரிவித்துள்ளனர். மேற்கண்ட பகுப்பாய்வின் அடிப்படையில், இதற்கு பல காரணங்கள் இருப்பதாக நான் நினைக்கிறேன்:
A. துகள் மேற்பரப்பு மென்மையாக இல்லை, கீறல் சுத்தமாக இல்லை, மேலும் துகள்கள் தளர்வானவை மற்றும் தூள் உற்பத்திக்கு ஆளாகின்றன;
B. திரையை தரப்படுத்துவதன் மூலம் முழுமையடையாத திரையிடல், அடைபட்ட திரை வலை, ரப்பர் பந்துகளின் கடுமையான தேய்மானம், பொருந்தாத திரை வலை துளை போன்றவை;
C. முடிக்கப்பட்ட தயாரிப்பு கிடங்கில் நிறைய சாம்பல் எச்சம் உள்ளது, மேலும் அனுமதி முழுமையாக இல்லை;
D. பேக்கேஜிங் மற்றும் எடையிடும் போது தூசி அகற்றுவதில் மறைக்கப்பட்ட ஆபத்துகள் உள்ளன;
கையாளுதல் நடவடிக்கைகள்:
A. சூத்திர அமைப்பை மேம்படுத்தவும், ரிங் டையை நியாயமான முறையில் தேர்ந்தெடுக்கவும், சுருக்க விகிதத்தை நன்கு கட்டுப்படுத்தவும்.
B. கிரானுலேஷன் செயல்பாட்டின் போது, மூலப்பொருட்களை முழுமையாக பழுக்க வைத்து மென்மையாக்க, வெப்பநிலைப்படுத்தும் நேரம், உணவளிக்கும் அளவு மற்றும் கிரானுலேஷன் வெப்பநிலையைக் கட்டுப்படுத்தவும்.
C. துகள் குறுக்குவெட்டு சுத்தமாக இருப்பதை உறுதிசெய்து, எஃகு துண்டுகளால் ஆன மென்மையான வெட்டும் கத்தியைப் பயன்படுத்தவும்.
D. தர நிர்ணயத் திரையைச் சரிசெய்து பராமரிக்கவும், மேலும் நியாயமான திரை உள்ளமைவைப் பயன்படுத்தவும்.
E. முடிக்கப்பட்ட தயாரிப்பு கிடங்கின் கீழ் இரண்டாம் நிலை திரையிடல் தொழில்நுட்பத்தைப் பயன்படுத்துவது தூள் உள்ளடக்க விகிதத்தை வெகுவாகக் குறைக்கும்.
F. முடிக்கப்பட்ட தயாரிப்பு கிடங்கு மற்றும் சுற்றுகளை சரியான நேரத்தில் சுத்தம் செய்வது அவசியம். கூடுதலாக, பேக்கேஜிங் மற்றும் தூசி அகற்றும் சாதனத்தை மேம்படுத்துவது அவசியம். தூசி அகற்றுவதற்கு எதிர்மறை அழுத்தத்தைப் பயன்படுத்துவது சிறந்தது, இது மிகவும் சிறந்தது. குறிப்பாக பேக்கேஜிங் செயல்பாட்டின் போது, பேக்கேஜிங் தொழிலாளி தொடர்ந்து பேக்கேஜிங் அளவின் இடையக ஹாப்பரிலிருந்து தூசியைத் தட்டி சுத்தம் செய்ய வேண்டும்..
5, துகள் நீளம் மாறுபடும்
1. தினசரி உற்பத்தியில், குறிப்பாக 420 க்கு மேல் உள்ள மாடல்களுக்கு, கட்டுப்பாட்டில் அடிக்கடி சிரமங்களை எதிர்கொள்கிறோம். இதற்கான காரணங்கள் தோராயமாக பின்வருமாறு சுருக்கப்பட்டுள்ளன:
(1) கிரானுலேஷனுக்கான உணவளிக்கும் அளவு சீரற்றது, மேலும் வெப்பநிலை விளைவு பெரிதும் ஏற்ற இறக்கமாக இருக்கும்.
(2) அச்சு உருளைகளுக்கு இடையில் சீரற்ற இடைவெளி அல்லது வளைய அச்சு மற்றும் அழுத்த உருளைகளின் கடுமையான தேய்மானம்.
(3) வளைய அச்சின் அச்சு திசையில், இரு முனைகளிலும் வெளியேற்ற வேகம் நடுவில் இருப்பதை விட குறைவாக உள்ளது.
(4) வளைய அச்சின் அழுத்தத்தைக் குறைக்கும் துளை மிகப் பெரியது, மேலும் திறப்பு விகிதம் மிக அதிகமாக உள்ளது.
(5) வெட்டும் கத்தியின் நிலை மற்றும் கோணம் நியாயமற்றது.
(6) கிரானுலேஷன் வெப்பநிலை.
(7) ரிங் டை கட்டிங் பிளேட்டின் வகை மற்றும் பயனுள்ள உயரம் (பிளேடு அகலம், அகலம்) தாக்கத்தை ஏற்படுத்துகின்றன.
(8) அதே நேரத்தில், சுருக்க அறைக்குள் மூலப்பொருட்களின் விநியோகம் சீரற்றதாக உள்ளது.
2. தீவனம் மற்றும் துகள்களின் தரம் பொதுவாக அவற்றின் உள் மற்றும் வெளிப்புற குணங்களின் அடிப்படையில் பகுப்பாய்வு செய்யப்படுகிறது. ஒரு உற்பத்தி அமைப்பாக, தீவன துகள்களின் வெளிப்புற தரம் தொடர்பான விஷயங்களுக்கு நாம் அதிகம் ஆளாகிறோம். உற்பத்திக் கண்ணோட்டத்தில், நீர்வாழ் தீவன துகள்களின் தரத்தை பாதிக்கும் காரணிகளை தோராயமாக பின்வருமாறு சுருக்கமாகக் கூறலாம்:
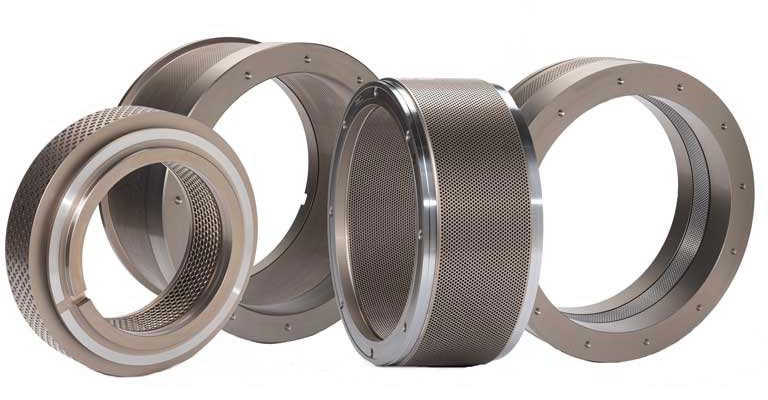
(1) நீர்வாழ் தீவனத் துகள்களின் தரத்தில் சூத்திரங்களின் வடிவமைப்பு மற்றும் அமைப்பு நேரடி தாக்கத்தை ஏற்படுத்துகிறது, இது மொத்தத்தில் தோராயமாக 40% ஆகும்;
(2) நொறுக்கலின் தீவிரம் மற்றும் துகள் அளவின் சீரான தன்மை;
(3) வளைய அச்சின் விட்டம், சுருக்க விகிதம் மற்றும் நேரியல் வேகம் ஆகியவை துகள்களின் நீளம் மற்றும் விட்டத்தில் தாக்கத்தை ஏற்படுத்துகின்றன;
(4) வளைய அச்சின் சுருக்க விகிதம், நேரியல் வேகம், தணித்தல் மற்றும் வெப்பநிலைப்படுத்தும் விளைவு மற்றும் துகள்களின் நீளத்தில் வெட்டும் கத்தியின் செல்வாக்கு;
(5) மூலப்பொருட்களின் ஈரப்பதம், வெப்பநிலைப்படுத்தும் விளைவு, குளிர்வித்தல் மற்றும் உலர்த்துதல் ஆகியவை முடிக்கப்பட்ட பொருட்களின் ஈரப்பதம் மற்றும் தோற்றத்தில் தாக்கத்தை ஏற்படுத்துகின்றன;
(6) உபகரணங்கள், செயல்முறை காரணிகள் மற்றும் தணித்தல் மற்றும் வெப்பநிலை விளைவுகள் துகள் தூள் உள்ளடக்கத்தில் தாக்கத்தை ஏற்படுத்துகின்றன;
3. கையாளுதல் நடவடிக்கைகள்:
(1) துணி ஸ்கிராப்பரின் நீளம், அகலம் மற்றும் கோணத்தை சரிசெய்து, தேய்ந்து போன ஸ்கிராப்பரை மாற்றவும்.
(2) சிறிய அளவிலான தீவனம் காரணமாக, உற்பத்தியின் தொடக்கத்திலும் முடிவிலும் வெட்டும் பிளேட்டின் நிலையை சரியான நேரத்தில் சரிசெய்வதில் கவனம் செலுத்துங்கள்.
(3) உற்பத்திச் செயல்பாட்டின் போது, நிலையான உணவு விகிதம் மற்றும் நீராவி விநியோகத்தை உறுதி செய்யவும். நீராவி அழுத்தம் குறைவாக இருந்தால் மற்றும் வெப்பநிலை உயர முடியாவிட்டால், அதை சரியான நேரத்தில் சரிசெய்ய வேண்டும் அல்லது நிறுத்த வேண்டும்.
(4) இடையே உள்ள இடைவெளியை நியாயமாக சரிசெய்யவும்உருளை ஓடு. புதிய அச்சுகளைப் புதிய உருளைகளுடன் பின்பற்றவும், மேலும் தேய்மானம் காரணமாக பிரஷர் ரோலர் மற்றும் ரிங் மோல்டின் சீரற்ற மேற்பரப்பை உடனடியாக சரிசெய்யவும்.
(5) வளைய அச்சுகளின் வழிகாட்டி துளையைச் சரிசெய்து, அடைபட்ட அச்சு துளையை உடனடியாக சுத்தம் செய்யவும்.
(6) வளைய அச்சுகளை வரிசைப்படுத்தும்போது, அசல் வளைய அச்சுகளின் அச்சு திசையின் இரு முனைகளிலும் உள்ள மூன்று வரிசை துளைகளின் சுருக்க விகிதம் நடுவில் உள்ளதை விட 1-2 மிமீ குறைவாக இருக்கலாம்.
(7) 0.5-1 மிமீ தடிமன் கட்டுப்படுத்தப்பட்ட மென்மையான வெட்டும் கத்தியைப் பயன்படுத்தவும், முடிந்தவரை கூர்மையான விளிம்பை உறுதி செய்யவும், இதனால் அது வளைய அச்சுக்கும் அழுத்த உருளைக்கும் இடையிலான வலையமைப்பில் இருக்கும்.
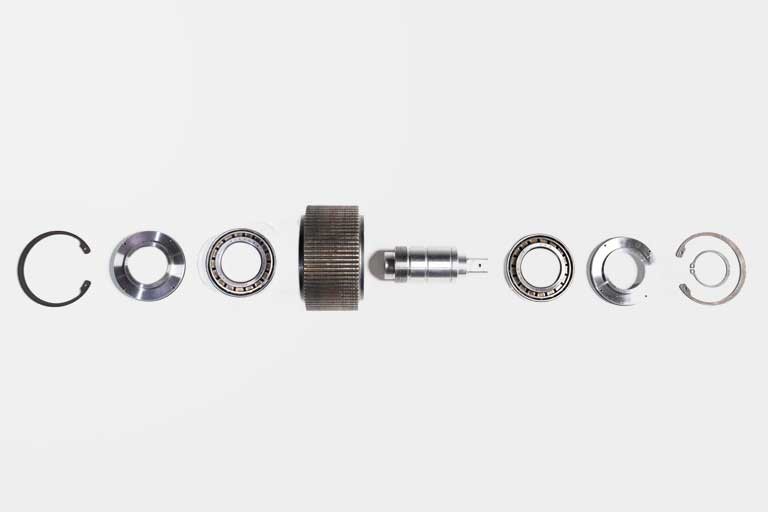
(8) வளைய அச்சின் செறிவுத்தன்மையை உறுதிசெய்து, கிரானுலேட்டரின் சுழல் இடைவெளியை தவறாமல் சரிபார்த்து, தேவைப்பட்டால் அதை சரிசெய்யவும்.
6, சுருக்கம் கட்டுப்பாட்டு புள்ளிகள்:
1. அரைத்தல்: அரைப்பதன் நுணுக்கம் விவரக்குறிப்புத் தேவைகளுக்கு ஏற்ப கட்டுப்படுத்தப்பட வேண்டும்.
2. கலவை: பொருத்தமான கலவை அளவு, கலவை நேரம், ஈரப்பதம் மற்றும் வெப்பநிலை ஆகியவற்றை உறுதி செய்வதற்காக மூலப்பொருள் கலவையின் சீரான தன்மையைக் கட்டுப்படுத்த வேண்டும்.
3. முதிர்ச்சி: பஃபிங் இயந்திரத்தின் அழுத்தம், வெப்பநிலை மற்றும் ஈரப்பதம் கட்டுப்படுத்தப்பட வேண்டும்.
துகள் பொருளின் அளவு மற்றும் வடிவம்: சுருக்க அச்சுகள் மற்றும் வெட்டும் கத்திகளின் பொருத்தமான விவரக்குறிப்புகள் தேர்ந்தெடுக்கப்பட வேண்டும்.
5. முடிக்கப்பட்ட தீவனத்தின் நீர் உள்ளடக்கம்: உலர்த்துதல் மற்றும் குளிரூட்டும் நேரம் மற்றும் வெப்பநிலையை உறுதி செய்வது அவசியம்.
6. எண்ணெய் தெளித்தல்: எண்ணெய் தெளிப்பின் துல்லியமான அளவு, முனைகளின் எண்ணிக்கை மற்றும் எண்ணெயின் தரம் ஆகியவற்றைக் கட்டுப்படுத்துவது அவசியம்.
7. திரையிடல்: பொருளின் விவரக்குறிப்புகளுக்கு ஏற்ப சல்லடையின் அளவைத் தேர்ந்தெடுக்கவும்.
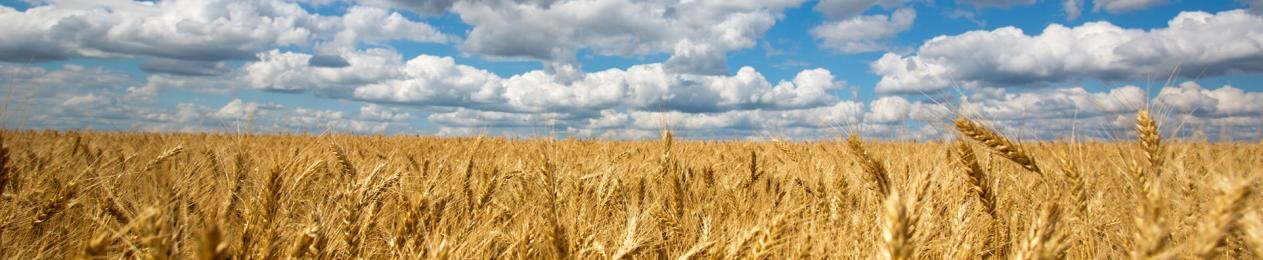
இடுகை நேரம்: நவம்பர்-30-2023